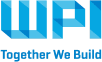
LOCATION
Headquartered in Portland, OR, with 11 regions across the U.S.
CONTRACTOR TYPE
Specialty
TRADE
Drywall, Acoustical, Fireproofing, Prefab
NO. OF EMPLOYEES
1,500+ field employees
ERP Integration

Building Excellence from the Ground Up: Meet Western Partitions, Inc
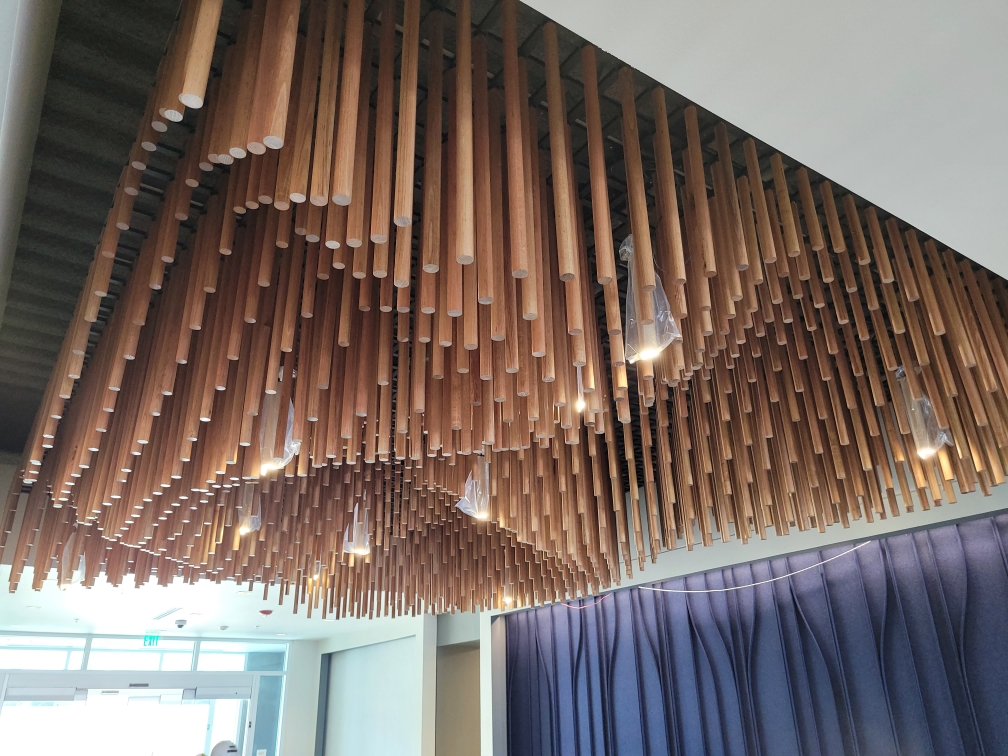
Western Partitions, Inc. (WPI) has spent decades delivering quality craftsmanship and efficient construction. With expertise in metal framing, drywall, acoustical ceilings, exterior insulation finishing systems (EIFS), plaster, and fireproofing, the company tackles major projects in healthcare, education, and data centers. Operating across 11 regional offices with over 1,500 field employees, WPI takes pride in running smooth and efficient job sites. As the company continued to expand, tracking labor hours, verifying clocked time, and managing payroll across multiple projects became more complex.
CHALLENGES
Why Manual Crew Time Entry Doesn’t Work
With a growing workforce and multiple projects happening across different regions, WPI’s commitment to operational efficiency required them to consider how to manage an increasingly complex labor force. Bill Everett, New Mexico Regional Manager and General Superintendent, saw firsthand how manual processes made time tracking more challenging as projects scaled. While WPI’s teams were highly skilled in the field, they needed a solution that would match their efficiency when it came to tracking labor hours and processing payroll. Challenges they faced before implementing SmartBarrel included:
Manual Processes Added Unnecessary Steps
Foremen were responsible for recording their crews’ hours on paper and submitting them weekly, creating a time gap between when work was performed and when it was verified. These records then had to be manually entered into the system, adding extra steps for both the field and the back office. With projects moving quickly, WPI wanted to reduce unnecessary back-and-forth and ensure accurate labor cost reporting in real-time.
“Really, we solely relied on the foreman. On smaller projects, a foreman would oversee a crew, with the crew size depending on the number of workers. On larger projects, a superintendent would manage multiple foremen, who were responsible for tracking time for their crews. They would then submit those records weekly. We were using paper and pen for tracking, and by Friday, we would enter everything into our field time entry system,” said Everett.
Ensuring Accuracy and Accountability
With WPI’s growth, making sure reported labor hours were verified continued to challenge the team. Errors happened more frequently, undermining efforts to get a clearer picture of project labor costs. Everett and his team needed a simple way to streamline the time-tracking process that allowed the field and payroll to maintain trust and accountability.
SOLUTION
A Seamless Transition to SmartBarrel
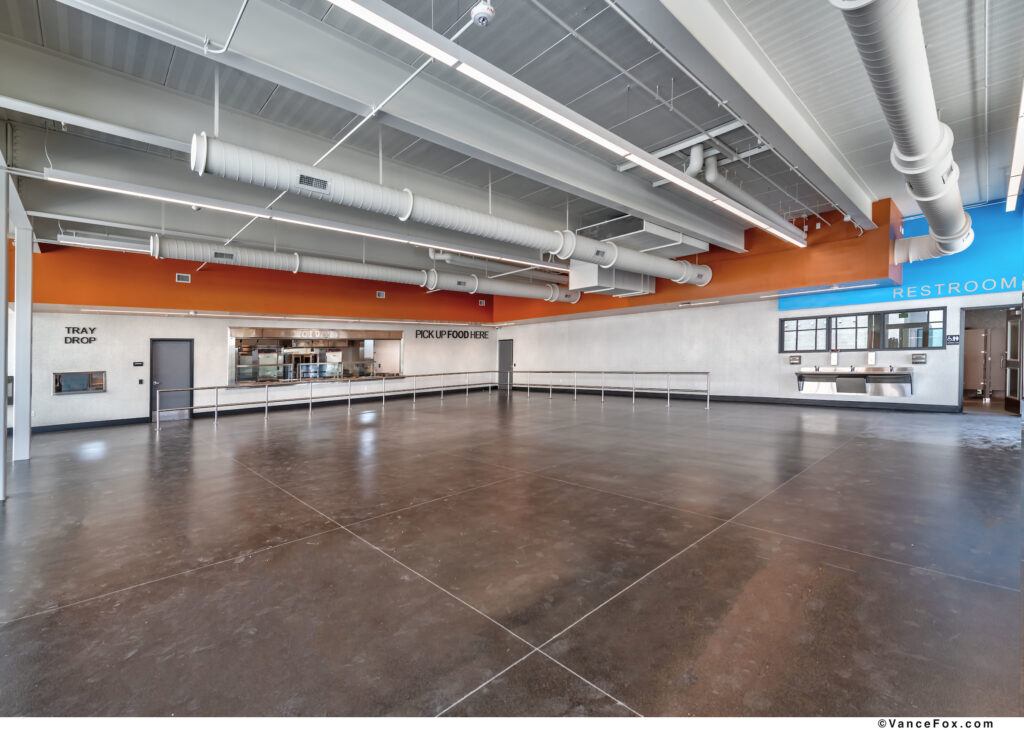
The Cares Campus Welcome Center serves as the central hub for the Nevada Cares Campus, providing essential services to the homeless and less fortunate. The project includes an 18,000-square-foot Resource Building, a remodeled structure, and a newly constructed 29,000-square-foot, two-story Intake Building.
The first location to implement SmartBarrel’s AI-powered biometric time tracking solution was their Phoenix division, which saw the potential for improved timekeeping accuracy and efficiency. As the benefits became clear, Everett tested the system on a WPI project in New Mexico and quickly saw its impact. What started as a small test became a regional standard, reinforcing WPI’s commitment to innovation and operational excellence.
"Phoenix introduced SmartBarrel first. Once they saw the cost-effectiveness and the savings, I figured we’d give it a try. I tested it on one project, then another, and another. Now, New Mexico uses it as a standard. If it’s not in SmartBarrel, you’re not getting paid. It really pushed the foremen to adopt it, and now they’re on board. I think we’ve been using it for close to a year," Everett stated.
After the initial test, Everett saw immediate improvements. The system’s biometric time tracking software and hardware devices that go on the jobsite replaced foremen having to be responsible for recording time for their crews, reducing errors and delays that came with paper timesheets and crew time entry.’
SmartBarrel’s real-time labor tracking provided attendance management, automatically recording hours worked, and reduced the need for foremen to manually track time and submit records. This change helped simplify payroll processing, cutting down on back-and-forth communication between the field and the office while also eliminating overreported hours. With clearer, more accurate data on labor costs, WPI was able to improve budget management and gain better visibility into jobsite operations.
As SmartBarrel continued to prove successful, Everett highlighted the company’s efforts to integrate with other systems to further streamline processes:
"We’re finalizing our approach to time entry, and SmartBarrel is a big part of that. We’re phasing out the old system and testing new processes that will integrate more smoothly with our existing tools. I’ve already seen a significant drop in reported hours, which shows how much more efficient and accurate the system is working," said Everett.
WPI is also finalizing the integration of SmartBarrel with Procore, which will provide even greater efficiencies in project management and time reporting. Once fully implemented, we anticipate further time savings and accuracy improvements across all projects.
Get Control of Your Time Tracking
RESULTS
Increased Payroll Accuracy and Time Savings
Key Metrics:
- Verifying timesheets used to take over an hour each week but now requires only 15 minutes, cutting the time spent by 75%.
- Timesheet errors affected 10-15% of entries submitted, but SmartBarrel has helped eliminate discrepancies, helping WPI achieve 100% error-free reporting.
- The overall payroll approval process has seen a 60% reduction in time, with a shift from a 5-hour manual process to just 2 hours, boosting payroll efficiency and freeing up time for other critical tasks.
Before SmartBarrel, WPI faced a 10-15% estimated error rate in timesheet entries, requiring time-consuming manual corrections. After SmartBarrel was implemented across projects, the WPI payroll team saw this error rate drop to nearly 0%. By automating its labor tracking system, WPI was able to receive greater accuracy and real-time labor data, virtually eliminating major timesheet discrepancies.
Streamlined Payroll and Increased Efficiency
The 75% reduction in time spent verifying timesheets has been a major win for WPI. “We spent over an hour verifying timesheets every week. Now, we spend 15 minutes at most,” Everett shared. This allowed the payroll team to be more productive and focus on other essential tasks. The increased efficiency also allowed WPI to be able to process payroll quicker, making sure workers get paid on time without delay.
Cost Savings and Better Visibility into Labor Costs
SmartBarrel generated significant cost savings, estimated at $1,000-$2,000 per project per month in labor costs. For the New Mexico region, these savings resulted in an estimated $36,000 in annual savings. With the real-time data from SmartBarrel, WPI could better manage and forecast labor costs, giving them much clearer insight into overall budget management.
“Part of my daily routine now is reviewing the daily reports from the previous day. I check who’s using SmartBarrel, which is most of our sites at this point. I go over clock-in and clock-out times, making sure there are no missed sign-ins or sign-outs. I know exactly who’s on-site and who isn’t every day.”
“I definitely think there’s added value beyond just the cost savings. We use the broadcast feature quite a bit now, too, because workers can check in and check out directly through it. It’s almost like a group chat, where you can send a message to the entire jobsite showing who was there for the day, the last seven days, or anyone who checked in at any time.”
These savings are based on the current SmartBarrel implementation. Once fully integrated with Procore, additional efficiency gains and time savings will be reflected in future updates.
Full Adoption and Long-Term Benefits
With SmartBarrel implemented across multiple projects in the Phoenix, New Mexico, and Reno regions, Everett and his team had a more expansive view of how labor was managed. The clear visibility into attendance and hours led to better accountability for both field workers and foremen. Everett highlighted that by implementing a strict policy around usage, the adoption rate was solidified, and communication improved. Now, after nearly a year, SmartBarrel has become the standard across these regions.
Get Control of Your Time Tracking
The SmartBarrel Advantage for Complex Projects
Under Bill Everett’s leadership, WPI streamlined its time tracking and payroll processes with SmartBarrel. By switching to automated time tracking, WPI eliminated errors, improved efficiency, and saw significant monthly cost savings. Everett’s proactive leadership and commitment to enforcing the new system drove full adoption, making SmartBarrel an essential tool for managing large-scale, complex projects.
Ready to modernize your timekeeping?
Contact us today to schedule a demo and see how SmartBarrel can eliminate inefficiencies, improve payroll accuracy, and help keep your projects on track.