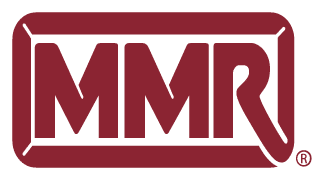
LOCATION
Baton Rouge, Louisiana
CONTRACTOR TYPE
Specialty Contractor
TRADE
Electrical, Instrumentation, Technical
NO. OF EMPLOYEES
8,500
Leading the Way Across High-Stakes Projects: Meet MMR Group
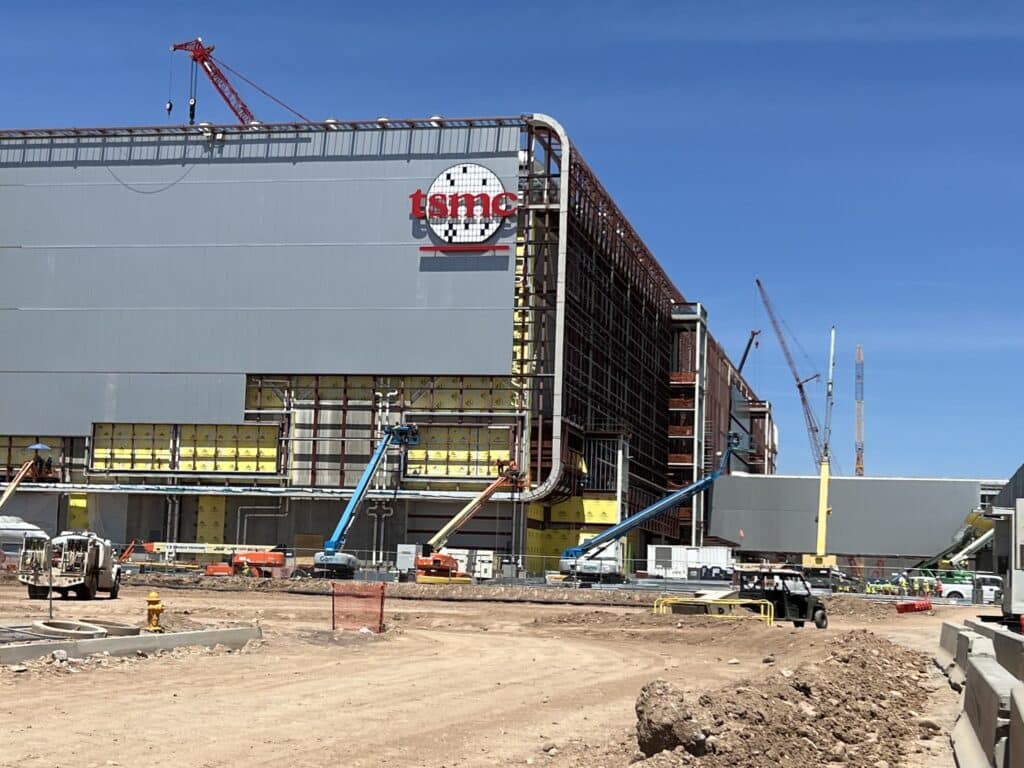
As the largest non-union electrical contractor in the U.S., MMR Group oversees a workforce of around 8,500 employees across North and South America. Known for handling high-stakes, large-scale projects, MMR is a major player in complex builds, including their work on the TSMC semiconductor plant in Phoenix, AZ. This $65 billion multi-year development project has MMR managing a $120 million electrical scope within the plant’s cleanroom areas. With a project of this scale, precise workforce management and strict control over labor accuracy were essential.
CHALLENGES
When Gate Log Systems Fall Short on Complex Projects
The TSMC semiconductor plant in Phoenix is a critical part of the U.S. push to boost domestic chip production, and it’s no small feat. MMR Group was brought in to handle a $120 million electrical scope, focusing on the specialized cleanroom environments essential for semiconductor manufacturing. With up to 400 MMR employees on-site at its peak, this project involved more than 10,000 workers across multiple shifts—putting pressure on MMR’s labor tracking and payroll systems.
Relying on the owner’s traditional gate log systems for timekeeping quickly proved inadequate for such a large and complex project. These systems couldn’t keep up with the scale, the volume of data, or the level of accuracy required to maintain payroll efficiency and control.
“We relied on the gate log system, but it didn’t give us the level of control we needed for such a complex project,” said Isaac Fincher, MMR’s Cost Engineer. “With hundreds of workers across multiple shifts, tracking hours accurately became a major challenge. The gate log wasn’t designed to handle this scale with the precision we needed.”
The gate log system led to recurring issues with missing or inaccurate hours, creating inefficiencies that drained administrative resources. MMR’s payroll team found themselves manually verifying entries and correcting discrepancies, adding significant stress to an already high-stakes project.
“There were too many instances where hours didn’t line up, and we had to go back and check each entry,” Fincher explained. “It took a lot of time and added stress for the team, who were already managing multiple tasks on a high-stakes project.”
SOLUTION
MMR Group Enhances Accuracy and Efficiency with AI-powered Biometric Time Tracking
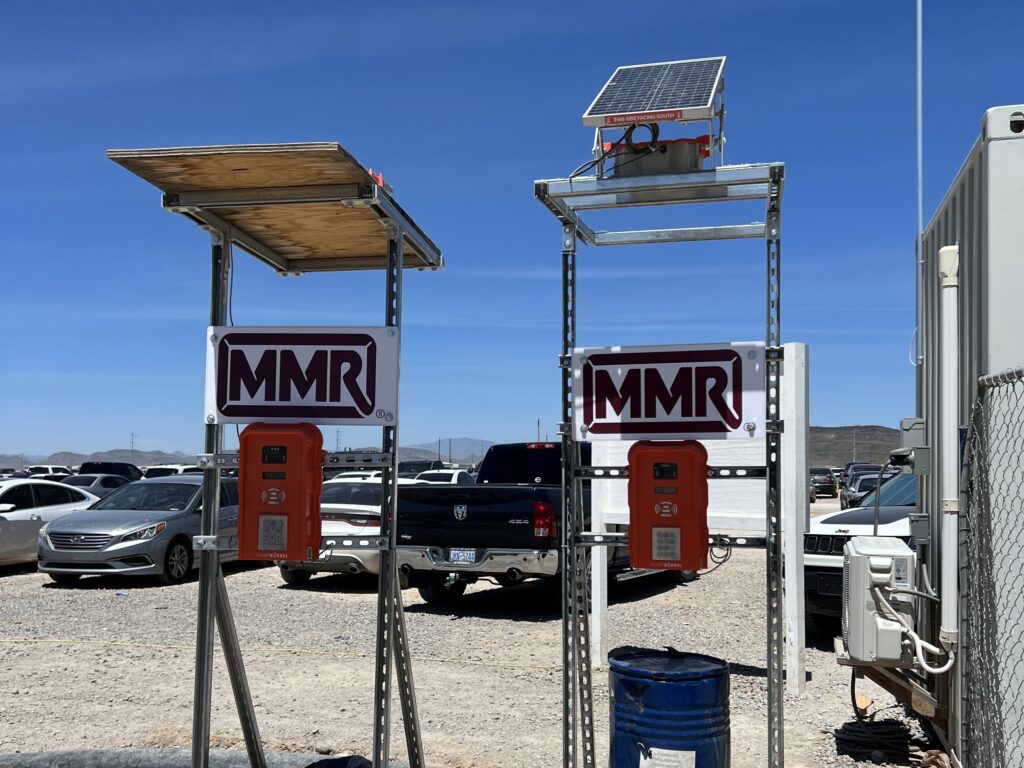
MMR implemented SmartBarrel to address the inaccuracies and lack of control with the gate log system and to use it as a verification tool to improve payroll data accuracy and employee accountability. With SmartBarrel’s biometric features like facial verification, photo ID, and geofencing, MMR gained the accuracy and control they needed to verify time entries and streamline attendance tracking.
“SmartBarrel gave us the extra layer of accuracy we needed,” said Fincher. “With facial verification and real-time data access, we could finally trust that the hours we logged were accurate. It cuts down the need for manual checks.”
SmartBarrel synced effortlessly with MMR’s Construction Management System (CMS), feeding real-time data directly into their payroll records. This setup helped MMR’s team spot and fix discrepancies on the spot, cutting down on time-consuming payroll corrections and keeping payroll processing quick and accurate.
“SmartBarrel allowed us to spot issues as they happened rather than scrambling to fix them after the fact,” Fincher noted. “This proactive approach saved us a lot of headaches and kept the project on track.”
RESULTS
20+ Hours Saved Every Week, and Payroll Accuracy Restored
MMR saw measurable improvements across time management, accountability, and cost savings, thanks to SmartBarrel’s accuracy and data integration:
20 Hours/Week Saved in Payroll Corrections: With SmartBarrel’s verification capabilities, MMR saved around 20 hours weekly by catching discrepancies early and preventing extra payroll work.
“We were saving at least 20 hours a week by not having to go back and correct payroll entries,” Fincher shared. “The time saved allowed us to focus on other critical areas of the project.”
4-5 Hours/Week Saved in Admin Time: SmartBarrel cut down administrative time for payroll verification by 4-5 hours each week, allowing payroll staff to focus on more strategic tasks.
“Instead of spending hours every week tracking down errors, our team could actually focus on more strategic work,” Fincher explained.
Increased Accountability and Reduced Time Theft: SmartBarrel’s tracking features reinforced punctuality, curbing early departures and late arrivals and fostering accountability.
“People started showing up on time because they knew we were tracking it closely,” Fincher noted. “It helped us keep everyone accountable and reduced time theft significantly.”
Better Data Accuracy and Retrieval: SmartBarrel’s integration with MMR’s CMS system improved data retrieval and validation, reducing the workload on payroll and creating a smoother reconciliation process.
“The integration with our system gave us instant access to all the data we needed, which made reconciling records so much faster and easier,” said Fincher. “SmartBarrel made everything smoother.”
These results demonstrate the significant efficiency gains and cost savings MMR achieved by supplementing its traditional gate log with SmartBarrel’s technology.
Powering the Future of Domestic Chip Production
The TSMC semiconductor plant in Phoenix isn’t just another big project. It’s a key part of the U.S.’s plan to bring chip manufacturing back home. As the demand for semiconductors grows, reducing reliance on overseas production is more important than ever. This project has become central to America’s goal of leading the way in semiconductor technology.
"This project is about more than just building a state-of-the-art manufacturing plant," said Isaac Fincher, MMR's Cost Engineer. "It's about strengthening America's position as a global leader in semiconductor technology. Our work here is contributing to that larger mission."
MMR’s $120 million electrical scope was critical to the success of this project. With their experience in handling complex, large-scale builds, MMR made sure that every detail was executed to perfection. Managing up to 400 employees on-site at peak demand required precision, and SmartBarrel played a key role in making sure everything ran smoothly.
"Semiconductor manufacturing requires an incredibly precise, controlled environment," Fincher explained. "Any lapses in workforce management could have cascading impacts, threatening the integrity of the entire facility. SmartBarrel gave us the tools to maintain that level of rigor and reliability."
What MMR achieved on this project isn’t just about what SmartBarrel helped them do internally. It’s about showing what U.S. construction companies can bring to the table in high-stakes projects like this one.
"This project is a testament to the expertise and innovation of U.S. construction companies," Fincher stated. "We're proud to be part of the team that's helping to secure America's semiconductor future."
The SmartBarrel Advantage for Complex Projects
SmartBarrel has proven essential for contractors seeking tighter control over labor tracking on high-demand projects and mega projects. For MMR Group, SmartBarrel filled critical gaps left by traditional owner-provided gate log systems, enabling real-time tracking, verified attendance, and accurate payroll processing across a multi-million-dollar job site.
“SmartBarrel allowed us to handle workforce tracking at the scale we needed without compromising on accuracy or efficiency,” Fincher concluded. “For any contractor looking to enhance labor tracking and cut down on manual work, it’s a game-changer.”
MMR’s experience shows how SmartBarrel’s advanced workforce management technology empowers contractors to boost productivity and achieve real savings on large-scale projects.
Ready to move beyond outdated timekeeping?
Discover how SmartBarrel can transform your job site management. Contact us today to schedule a demo and upgrade your time tracking with SmartBarrel.