SmartBarrel
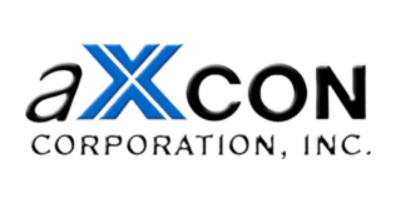
Axcon is a service company providing nationwide mechanical installation, on-site fabrication solutions, and services for the Supply Chain, Retail Distribution, Food and Beverage, Manufacturing and Material Handling industries. We maintain integrity throughout our business cycle and that means delivering on our promises, and doing what it takes to get the job done. We think it’s the right way to do business. Our customers agree, since they choose to collaborate with us on additional projects. Keeping our promise is not an option, it’s part of who we are.
LOCATION
CONTRACTOR TYPE
TRADE
NO. OF EMPLOYEES
Mechanical contractor boosts their win rate by 5% with insights and savings delivered from implementing SmartBarrel
Axcon is a nationwide mechanical installation company with on-site fabrication solutions and services for the supply chain, retail distribution, food and beverage, manufacturing, and material handling industries. With over 80 employees and more than 30 temporary workers, labor is their biggest expense and largest job cost item. Ensuring accurate trade time tracking is the secret ingredient to remaining competitive and winning new business. SmartBarrel helped shave an average monthly cost of $246 per employee and gave Axcon the insights they needed to deliver more accurate estimating, leading to a 5% increase in bids won.
BEFORE SMARTBARREL
The unforeseen Impact of Inaccurate Time Tracking
Prior to SmartBarrel, Supervisors entered their crew’s time – winging timesheets and approximating when employees showed up – usually in the employees’ favor. Don Schesny, SVP of Implementation at Axcon, stated: “Supervisors entered a flat 60 hours per week for each employee regardless of how many hours they actually worked.” Because field management wasn’t tracking employee time accurately, the executive team didn’t have reliable insights into productivity costs. The result was project overruns on labor, leading to 5-10% higher estimates on the next jobs they bid.
Searching For Solutions
Once Axcon identified the problem – the need for 100% accurate field time tracking – they worked on finding a simple solution that they could effortlessly deploy. Their criteria included:
- To-the-minute time tracking to leverage the data for improved future estimate accuracy,
- Easy to deploy at new job sites since they run 10-15 jobs per week,
- Easy for the field to use without any training lasting more than 3 minutes; and,
- Reduce payroll admin time through Integration into their project management tool – Procore.
SmartBarrel checked off all the boxes.
THE RESULTS
With SmartBarrel, Axcon now:
- Tracks workers’ time to the minute, from when they scan in to when they scan out of the job site.
- Gets new job sites up in 2 minutes.
- Onboards and trains new employees in 2 minutes.
- Saves one entire day processing payroll each week with full timesheet integration into Procore.
THE IMPACT
Improved Top and Bottom Lines
Immediately, workers went from working an average of 57 hours per week but earning 60 hours to earning precisely the time they worked. With an average wage rate of $41/hour, each employee earned an additional $246 per month they didn’t work. The 5% wage savings quickly translated to a 5% drop in costs on the job, which translated to a 5% drop in future estimated costs. Axcon became more competitive and increased its bid win rate by 5%. Deploying SmartBarrel has improved Axcon’s efficiencies, improving top and bottom lines.
Time Tracking Drives Cultural Accountability
Everything in the company changed once Axcon started using SmartBarrel for accurate time tracking tracking the workers’ time. Workers quickly realized they got paid for the hours they actually worked, none of which could be manipulated. Supervisors started having better conversations with their workers around arrival, departure, and lunch times, which resulted in more efficiency and renewed accountability as a cultural value. Managers started reporting actual time worked to executives who could make better decisions to drive more efficiency and profitability.
"SmartBarrel has brought about a positive culture change at Axcon. Supervisors now have real-time data on employee hours, enabling them to make informed decisions and drive productivity."
The most accurate time clock in construction.
Powered by biometrics and AI, SmartBarrel completely automates time tracking and guarantees 100% accuracy.
Other testimonials
SmartBarrel is proudly powered by WordPress